Onze productiemethode
- Home
- Productiemethode
De producten die wij maken zien er al jaren hetzelfde uit. Maar dat betekent niet dat we hebben stil gezeten. De productie is van een ambachtelijke wijze, via CNC frezen naar 3D printen geëvolueerd. Deze verandering is geheel zelf ontwikkeld om zodoende precies te blijven weten wat we maken. 100% op maat, milieuvriendelijk en in eigen beheer!
100% op maat met de 3D printer
Sinds 1995 maakt de familie Ekelschot de steunzolen 100% op maat. Dat wil zeggen dat de 3D afdruk van de voet ook de basis is van de vorm van de zool. In de loop der jaren heeft deze methode zich steeds verder ontwikkeld, waarbij technologische vooruitgang een belangrijke rol heeft gespeeld. Zo hebben we jaren lang gebruik gemaakt van CNC techniek om de benodigde zolen uit bijvoorbeeld een blok kurk uit te frezen.
Begin 2022 hebben we geïnvesteerd in 3D-printers die specifiek geschikt zijn voor gebruik voor onze toepassing. Omdat de printers in feite van alles kunnen maken, was het nodig om het proces te ontwikkelen specifiek voor onze producten. Deze ontwikkeling en de praktijktests hebben ongeveer een jaar in beslag genomen. Zodoende konden we vanaf begin 2023 de 3D geprinte therapiezolen in de praktijk toepassen.
Het doel was om onze eigen 3D-technologie te blijven benutten en ervoor te zorgen dat bestaande patiënten geen verschil zouden merken in de behandeling. Uiteindelijk is dit zo goed gegaan dat deze deze techniek heel snel de plaats heeft ingenomen van de gebruikelijke technieken.
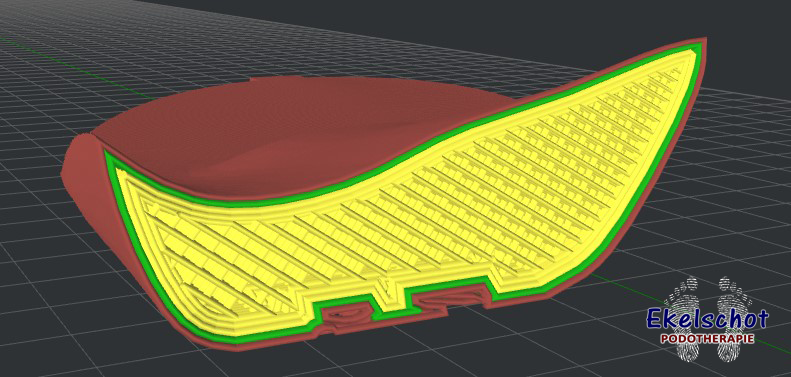
Hoe verloopt het productieproces?
Nadat al uw maten zijn opgenomen bij het podotherapeutische onderzoek wordt de 3D scan van uw voet gebruikt om een digitaal model van uw therapiezolen te maken. In dit model worden alle elementen en correcties aangebracht die voor u nodig zijn.
Als het model klaar is, dan wordt deze door de computer omgerekend naar een bestand met instructies voor de 3D printer. Is er een extra paar nodig? Dan kunnen we deze identiek produceren.
Dankzij de 3D-printtechnologie kunnen we niet alleen de buitenzijde, maar ook de binnenzijde van de zolen vormgeven. Hierdoor kunnen we zolen produceren die zowel stevig als zacht zijn, afhankelijk van de specifieke behoeften. Het vermogen om ook de interne structuur te bepalen resulteert in een verminderd gewicht en een efficiënter gebruik van materialen.
Het gebruikte materiaal is flexibel en heeft de kenmerken van een “normale” therapiezool.
Het gebruik van 3D-printen resulteert in aanzienlijk lager energieverbruik en vermindert afval met meer dan 95%. Deze bijkomende voordelen zijn van grote waarde voor ons en onderstrepen ons streven naar duurzame productieprocessen.
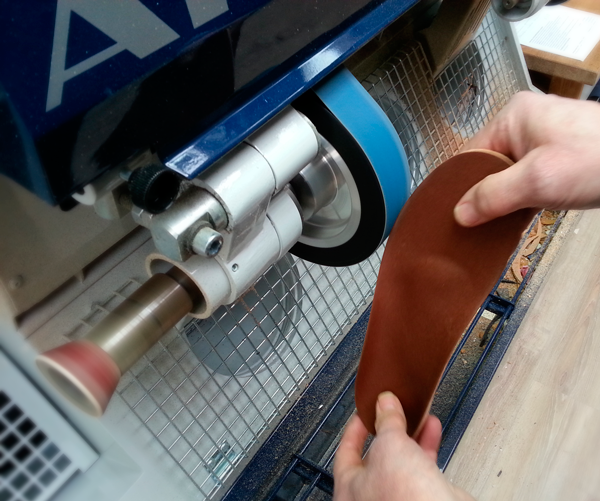
Na het voltooien van het printproces van de 3D-printer, gaan we verder met het afwerken van uw zolen. Eventuele dempingen worden zorgvuldig met de hand aangebracht voor optimale comfort en pijnverlichting.
Vervolgens worden de zolen bekleed met ademend materiaal en ondergaan ze een grondige kwaliteitscontrole.
Zodra dit proces voltooid is, zijn uw zolen gereed voor levering!